How Albatros Logistics uses Cloudempiere
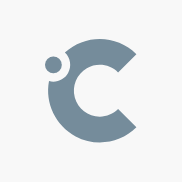
02.11.2015
The Albatros Logistics Ltd. business is specialized in automotive and electronics sectors. Its mainly deals with the transportation of materials to and from European and Asian countries and with warehouse management.
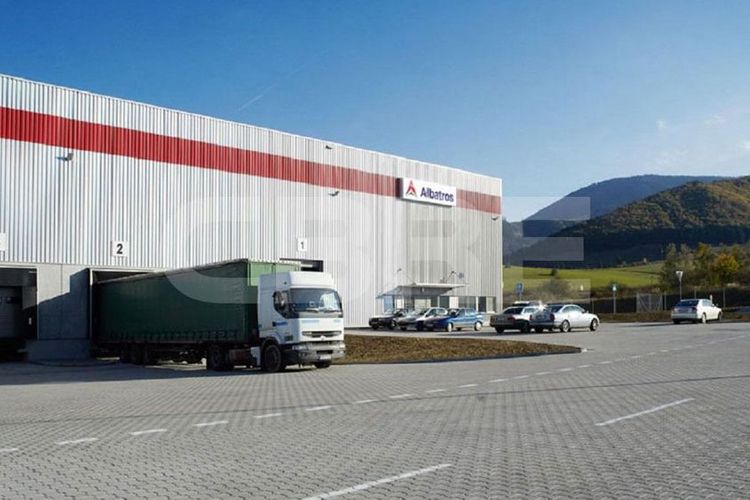
The company is building a net of warehouses in central Europe. The first basic step is to offer to outsource a warehousing solution for SEJONG Slovakia, an exhaust manufacturer for KIA Slovakia.
Entering
The basic concept was to design processes that can implement WMS (Warehouse Management System) into Warehouse’s operations management considering the specifications of the orderer and SEJONG Slovakia, its main customer.
Within the quality policy, the customer is being audited by KIA 5* which is a quality guarantee of company KIA Slovakia. It is obliged to keep all internal and external/ outsourced processes on the top level.
Choosing the supplier
Albatros Logistics Ltd. picked multiple suppliers that were presenting their ideas. They selected Cloudempiere Slovakia Ltd. based on the criteria set by SEJONG.
Basic internal processes of the customer
The subject of storage is a specific material needed for manufacturing exhausts assembled in Korea and then shipped to Slovakia for further processing. The material is packed into pre-destined trolleys exported to assembly lines and then processed during a given manufacturing strategy. The final products – exhausts are delivered on time to the KIA company.
Warehouse specifics
- 2000 pallet positions
- Area of 3000m2
Warehouse type
- High Rack system
- 4 docs/gates
- 10 warehouse operators
- 2 shift leaders
- 2 shift operation
Project scope and implementation
The project was to design and implement the hardware structure of IT including wireless coverage of the warehouse, rack labeling, and information systems.
Stages
- Analyze/Plan
- Run basic WMS (3weeks)
- Prototype, Testing (1 month)
- Users` training
- Prepare for 5* audit
- Reach 5* audit
- Active customer support
- Remote users support
Future
- To reach new businesses in the Czech Republic and Korea
- To install LCD boards for displaying inbound/outbound (current status)
- To implement further WMS solutions in other sectors
WMS Layout
The warehouse is divided into logical units (areas, sections). The smallest unit is called the location. The rack system is divided into other zones by weight: Normal Storage, Open Pallets, and Damaged Parts.
Material flow: Inbound => High Rack => Working Center => Delivery and Open Pallets.
Inbound
Inbound pre-alerts are received via e-mail and imported into WMS by a simple Excel file. The pre-alerts are processed in WMS when LOTs (list of tables/batches), as well as handling units, are generated for storage alerts.
Receive and put-away works upon defined Inbound strategy. WMS suggests locations for pallet placing considering the material type, dimensions, and weight. Pallets are then placed to corresponding locations based on the put-away lists.
Outbound
Outbound alerts are created on the daily basis and imported into WMS.
Export orders are transformed into ware- house’s orders. Shift-leader releases so-called picklists for warehousemen to pick the correct material for the orders. Picking is done upon manual picklists or by Unitech scanners.
Picking strategy
Picking is done via FIFO methodology. The system picks by whole pallets or only a certain amount of the material depending on its category. It is prioritized to pick first from Open Pellets and then from High Rack.
Packing/Exporting material
Pallets removed from the rack system are, based on types, properly repacked into trolleys and scanned (labels are printed). The pallets are then moved to Staging Zone. The unpacked material is moved back to the Open Pallets zone.
Mr. Jeong, Albatros Founder